How to Slot a Warehouse
- Dr. Ed Frazelle
- Aug 4, 2020
- 3 min read
Updated: Sep 18, 2020
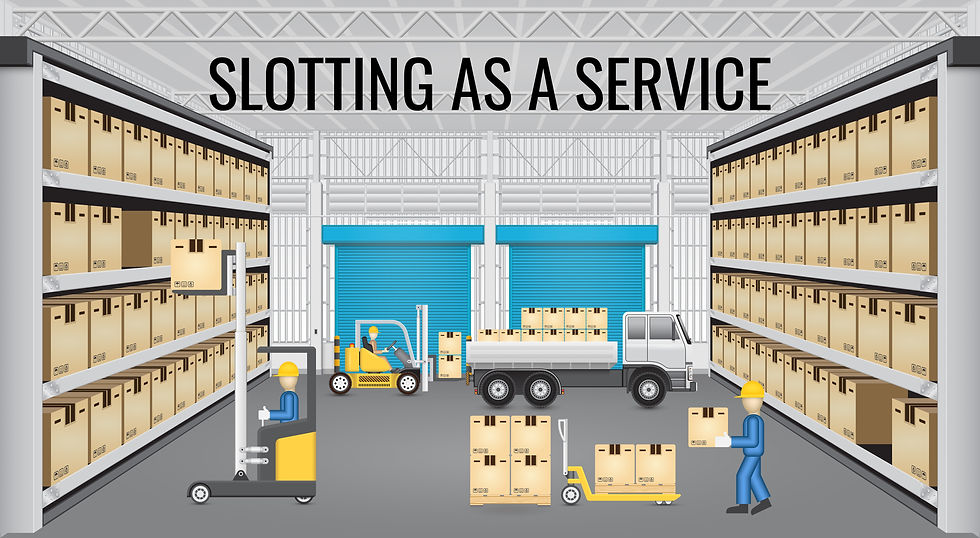
I started my work in slotting optimization over 30 years ago. From a DOS diskette to a desktop application to remote PC access, RightChain Slotting has become RightChain Slotting-as-a-Service. Incorporating CloudAi and integration with ERPs and WMS, our current subscription slotting optimization solutions include a slotting optimization API and a slotting optimization solution platform. The solutions are powered by RightChain.ai and incorporate a mix of artificial intelligence and conventional optimization methods. The solutions can be configured in a matter of hours.
Despite those new developments, the fundamentals of slotting have not changed. We only have easier, faster, and better ways to answer the same questions.
Over three decades we have been fortunate to slot many medium and large-scale warehouses and distribution centers at Avon, Baxter, Caterpillar, Clorox, Coca-Cola, Disney, GE, HP Hood, LL Bean, and Oxxo to name a few. That work and our current work is aimed at answering four fundamental questions for each SKU (stock keeping unit, aka part number). These four questions have not changed, and neither has the 23% to 38% reduction in picking and restocking costs associated with the right answers.
(1) Storage Mode Optimization. What storage mode should each SKU be assigned to? In pallet picking, the question is, "What combination and configuration of storage media (floor storage, single deep rack, double deep rack, push back rack, pallet flow rack, or mobile pallet rack) and vehicle type (man or unmanned counterbalance lift truck, reach truck, turret truck, or ASRS machine) minimize the storage and handling cost of each SKU?" In each picking, the question is, "Which of bin shelving, storage drawers, carton flow rack, horizontal carousels, vertical carousels, ASRS, or automated dispensing are the optimal picking mode for each SKU?"
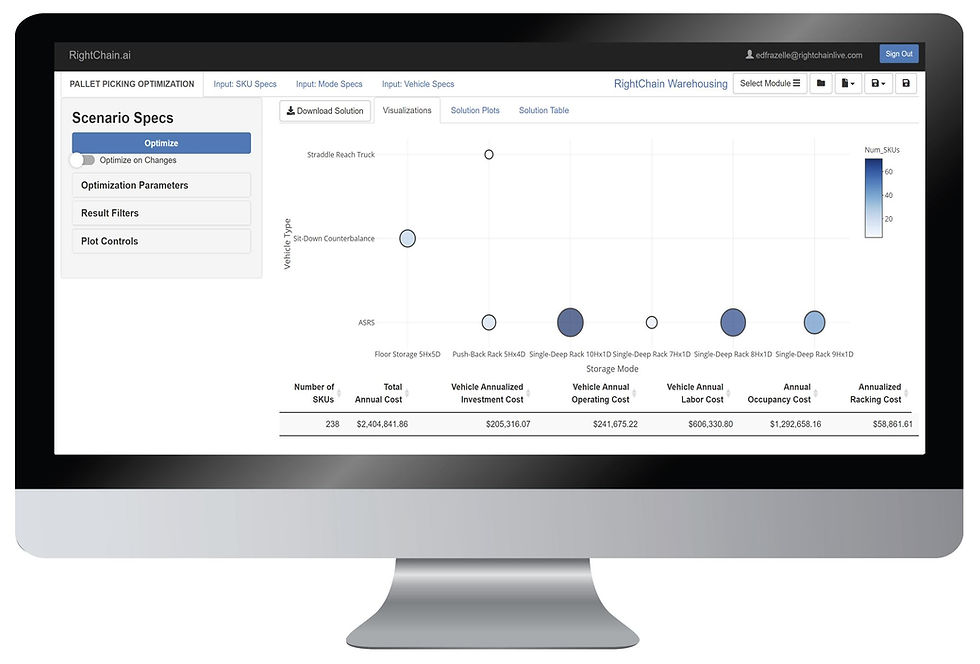
(2) Pick Face Optimization. How much space should be allocated to each SKU in its optimal mode? In pallet picking, the question is, "How many lanes and what lane depth is optimal for each SKU?" In each and case picking, the question is, "How much cubic space allocation is optimal for each SKU?"
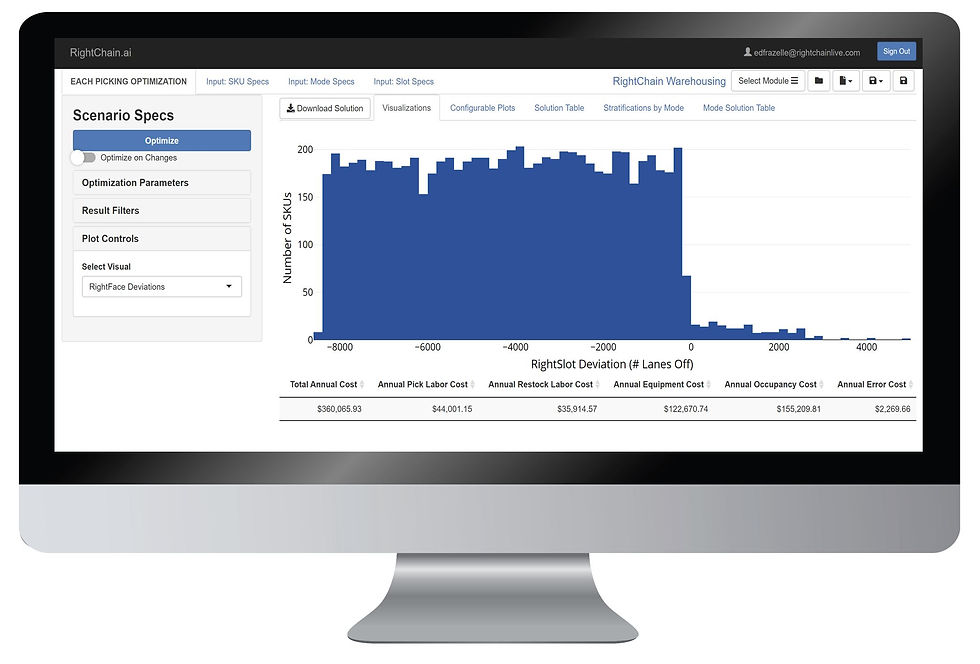
(3) Slot Location Optimization. Where, in its optimal storage mode, housed in its optimal pick face, should each SKU be located? The answer to this question takes into account travel time, product weight, ergonomics, demand correlation with other products, and picking accuracy.

(4) Re-slotting Optimization. Which SKUs should be re-slotted and when? Since each product's demand characteristics and each warehouse's order characteristics are dynamic, as soon as a warehouse is slotted optimally once, it needs to be re-slotted to maintain the gain of the original slotting optimization. Re-slotting optimization continuously computes the optimal slotting arrangement for a warehouse and continuously computes the optimal timing and relocation sequence for re-slotting warehouse products. Re-slotting optimization converts slotting optimization from a project to a process; a process that should be executed daily as re-slotting recommendations are developed from RightChain Slotting.

For 30+ years, our objective has been to help our clients minimize the sum cost of picking labor, restocking labor, occupancy, equipment, and errors via slotting optimization. We have always incorporated item popularity, cube, weight, demand correlation with other items, storage mode characteristics, and slot location characteristics. No matter the platform, by answering those four fundamental slotting questions correctly, RightChain Slotting has always reduced order picking and restocking costs by 23% to 38%.
Copyright: Dr. Ed Frazelle, RightChain Incorporated | All Rights Reserved
Web: RightChain.com
Comments